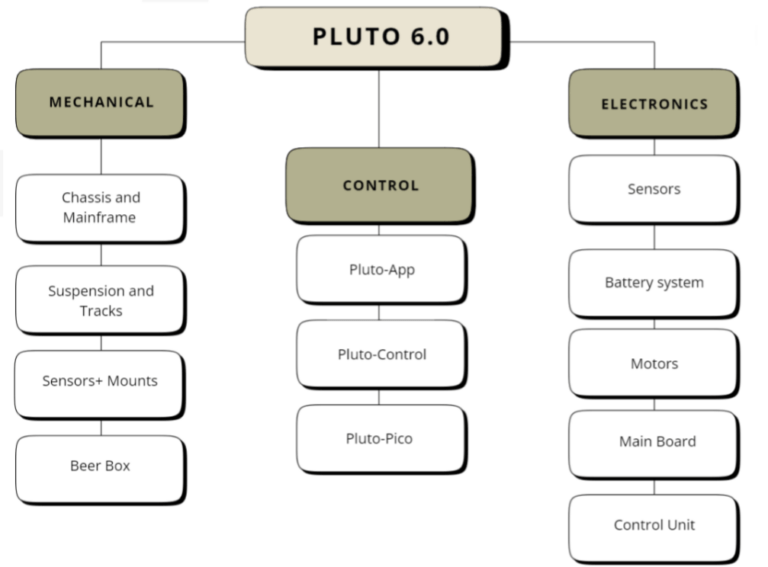
Subsystem Overview
The Pluto 6.0 System Model forms the foundation of this autonomous personal transportation project. It integrates three key subsystems—Mechanical, Electrical, and Control—that work together to ensure smooth and efficient operations. The system is designed to handle complex tasks such as autonomous transportation across a university campus, providing flexibility for future iterations and scalability.
Electrical System
The electrical system in Pluto 6.0 is engineered to efficiently manage power distribution, control safety mechanisms, and integrate all of the vehicle’s electronic components. At the heart of this system is a custom-designed mainboard, tailored specifically for Pluto 6.0, which ensures seamless energy management and operational safety. A standout feature is the advanced Battery Management System (BMS), which continuously monitors and optimizes energy usage, provides onboard charging capabilities, and guarantees that the vehicle always operates within safe limits.
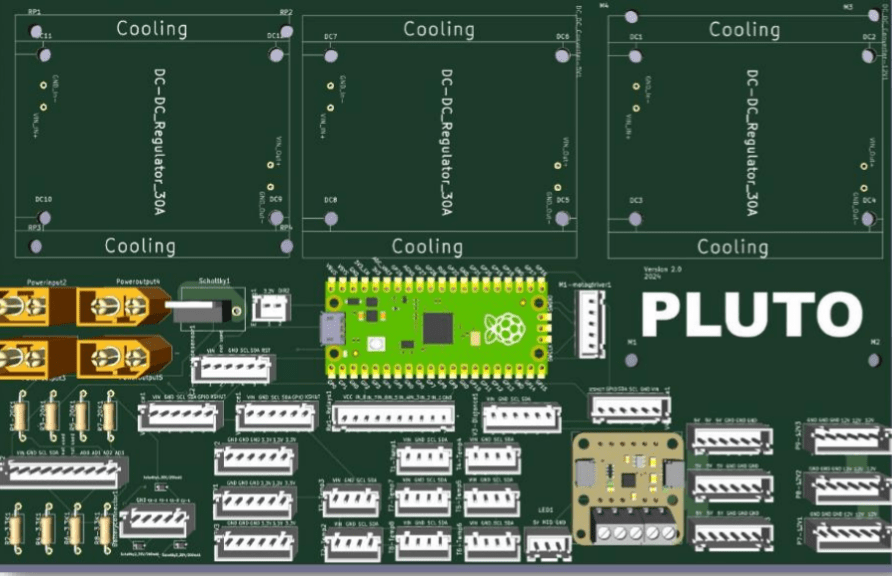
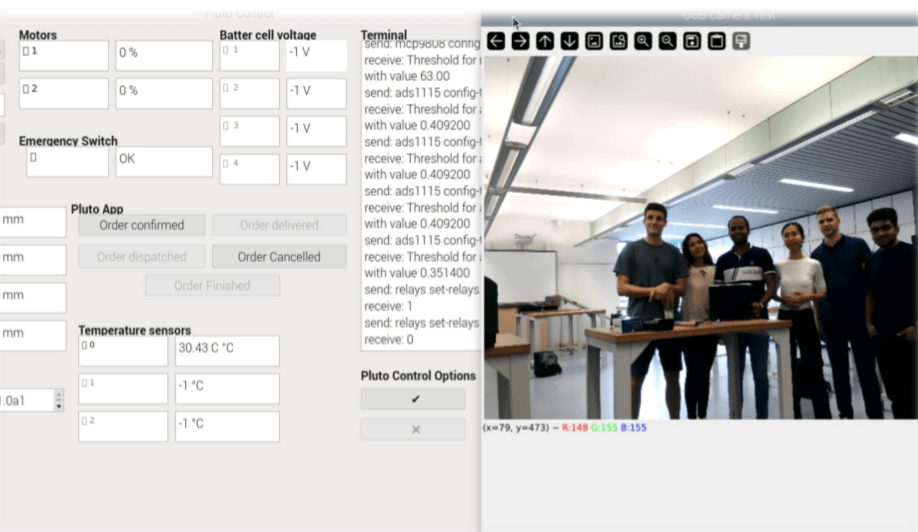
Control System
The control system of Pluto 6.0 allows for seamless operation, whether remotely or locally. Users can operate Pluto via an internet-based system using TeamViewer, providing access from anywhere in the world, or through a local network with RealVNC for faster, more responsive control. The user interface provides real-time feedback, displaying critical system information and error messages. This ensures that operators have full oversight of Pluto’s status and can issue commands with precision.
Mechanical System
The mechanical system of Pluto 6.0 serves as the structural backbone, responsible for maintaining stability and handling the physical aspects of the vehicle’s operation. This system includes critical components such as the chassis, suspension, and load-bearing elements. Each of these components has been optimized to ensure Pluto 6.0 can navigate varied terrains, carrying its intended payload with stability and durability. The design also emphasizes modularity, allowing for future upgrades to meet evolving performance requirements.
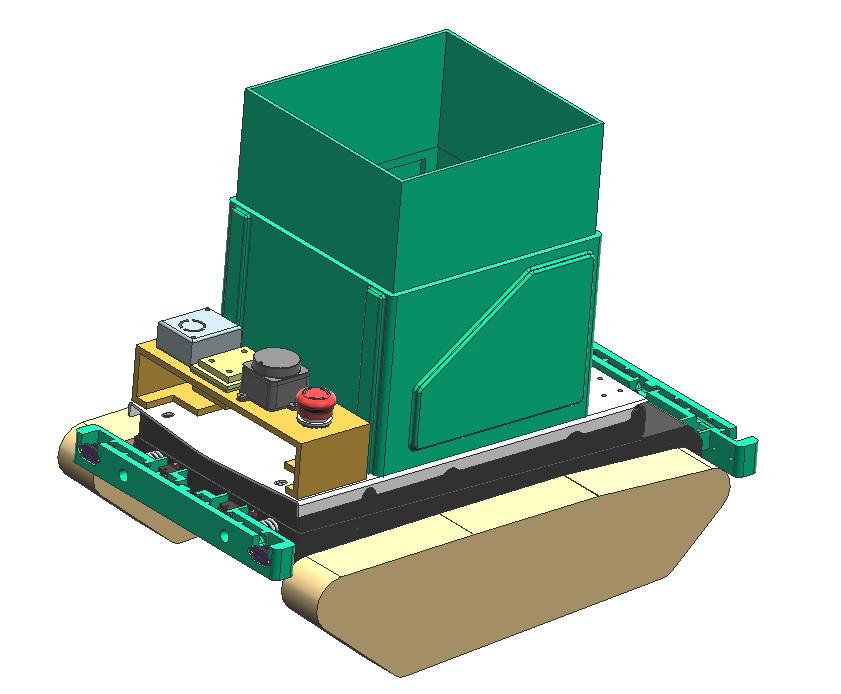
System Integration
The key to Pluto 6.0’s success is the seamless integration of its mechanical, electrical, and control systems. Each subsystem communicates efficiently through well-designed interfaces, ensuring smooth coordination. The modular approach of the system model not only supports current functionality but also allows for scalability and future enhancements, making Pluto 6.0 a flexible and adaptable autonomous solution.
Lessons learned
Throughout the development of Pluto 6.0’s System Model, several key lessons emerged. Early validation of each subsystem reduced development time, while iterative design processes allowed for refinement and optimization. Additionally, the importance of clear communication between subsystems became evident, as it ensured that integration was smooth and errors were minimized.
Conclusion
The Pluto 6.0 System Model is a robust, modular design that integrates mechanical, electrical, and control systems to create a reliable and flexible autonomous transportation vehicle. With seamless subsystem coordination and the capacity for future upgrades, Pluto 6.0 is built for adaptability, meeting current requirements while also paving the way for future innovation.